If you want to compound your recycled plastic in one step, this line will be your best choice, the first stage is recycling the extruder and then into parallel twin screw extruder compounding, The output capacity is from 200kg/h to 1000kg/h.
Features
Smart intelligent control.
Lower energy consumption, higher production.
High safety protection, protect personal safe and equipment safe.
Working Principle
- Feeding 1 is automatic according to customer requirements.
- Unit 2 the material is cut, mixed, heated, dried, degassed, densified and buffered.
- Next, the tangentially connected extruder is fi lled continuously with hot, pre-compacted material. In the extruder screw 3 the material is plasticised, homogenised and then cleaned in the fully automatic self-cleaning filter 4.
- The prepared and cleaned melt then goes via the melt pump 5 directly to the co-rotating, self-cleaning twin-screw extruder 6. With its excellent mixing and gas removal properties, this flexible part of the system can handle all compounding tasks.
- Besides the dosing of a wide variety of additives, high amounts of fillers and reinforcing agents 7 can be admixed. In the degassing zone 8 the compounded melt is degassed and moves to the respective tool 9 (e.g. POLYTEC hot die face pelletising system)
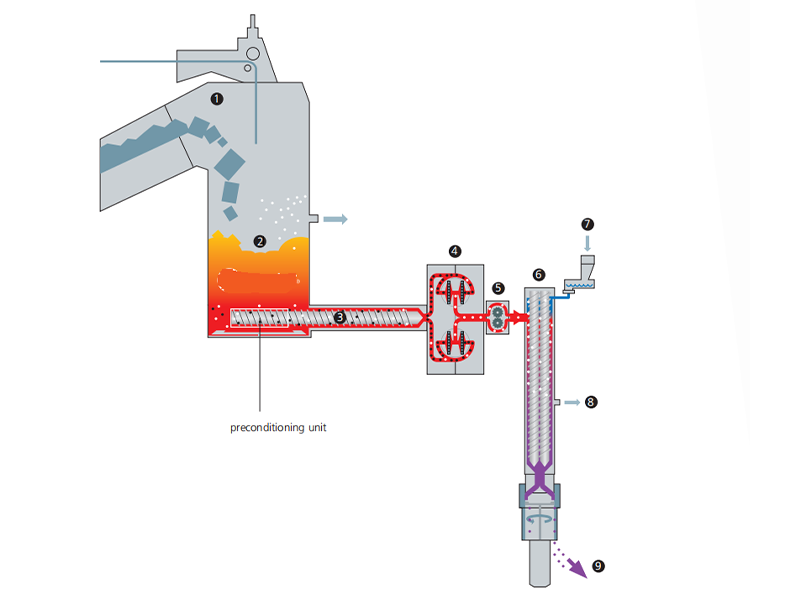
Technical Characteristics
Mode | Output capacity in kg/h* | Remark |
PTC100-65 | 300 | Examples of additives, fillers and reinforcing agents suitable for admixing |
PTC130-75 | 500 | |
PTC185-95 | 800-1000 |
Depending on material properties of the polymer (moisture content, print, degree of contamination, etc.) type and properties of the filling/reinforcing agent and the degree of filling.
Raw materials
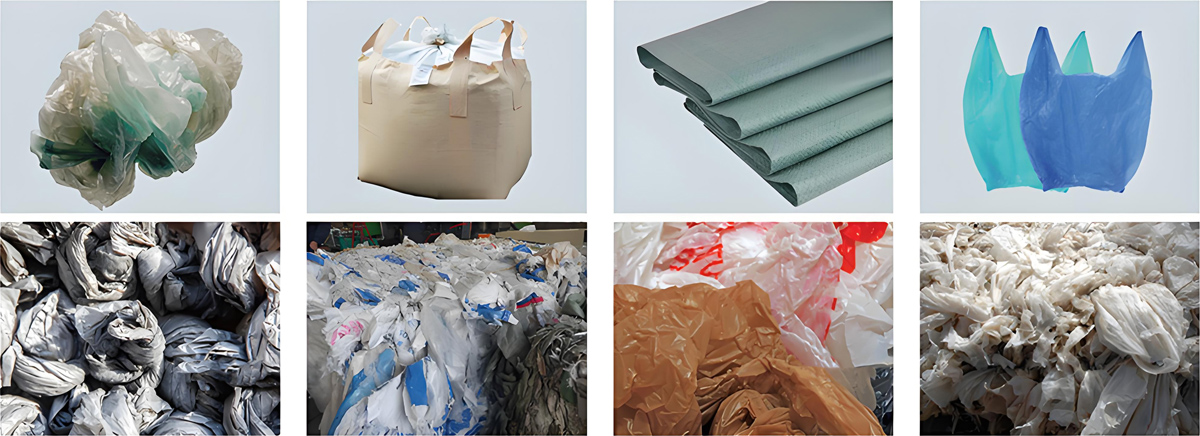
Products
